
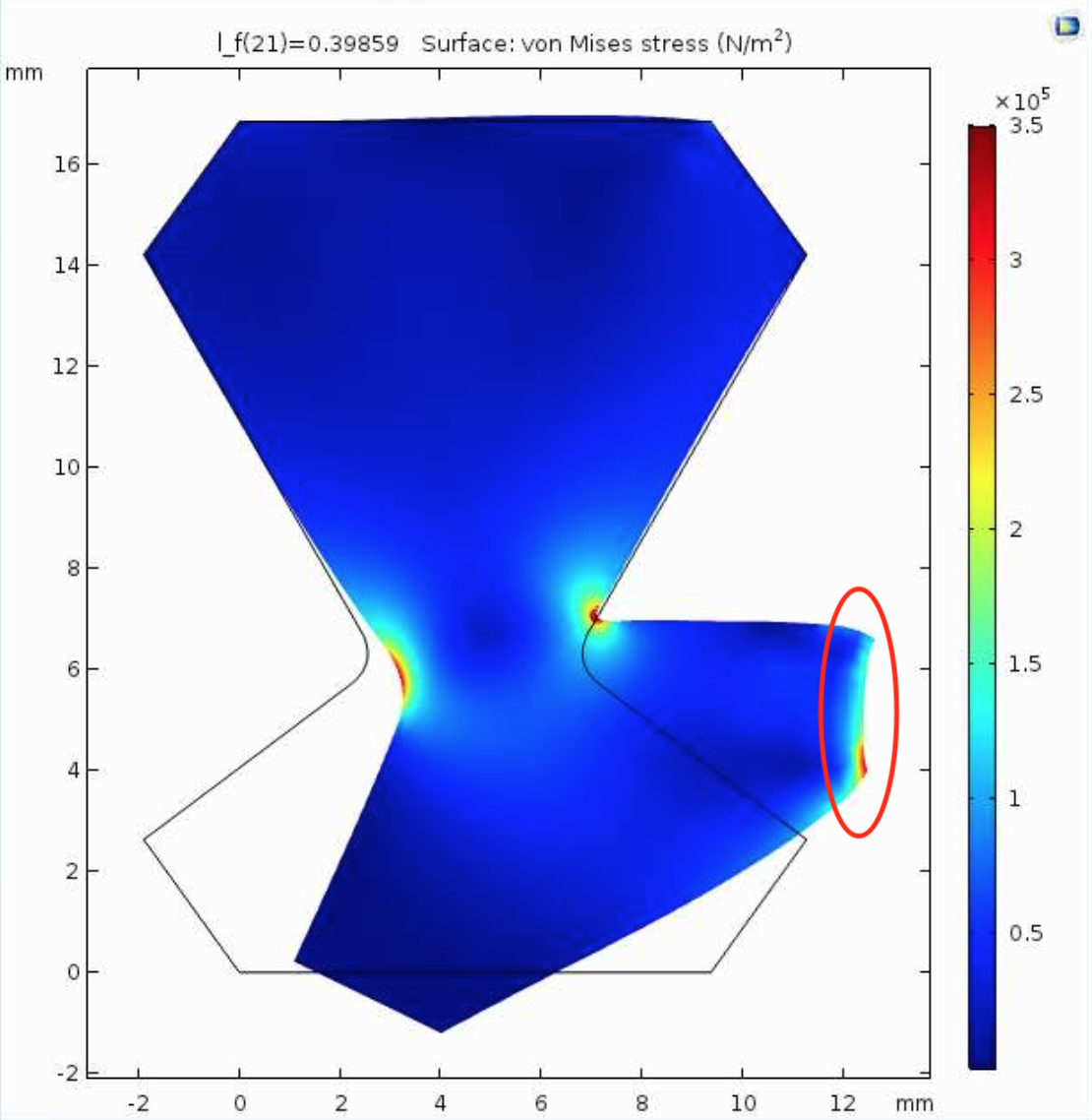


Through a series of experiments the maximum range of motion for the gripper is found to be 20mm, half of which is contributed by each finger. A prototype is realised through subtractive fabrication of the prototype. Crucial design standards factored in are low fabrication and material costs, parallel gripping motion of fingers, large finger displacement, low joint stress concentrations and low output forces. The feasibility of the design is examined through a series of numerical analysis and simulations on COMSOL platform. The monolithic model exhibits more lumped compliancy displacement than distributed compliancy. The gripper is monolithic in nature to properly accommodate flexure joints and also any further works in microelectronics process integration. Flexural joint mechanism is based on the intrinsic compliance of a material to achieve structural elastic deformation to achieve displacement. Flexural joint grippers with kiwifruit-size range of displacement are currently non-existent in the industry. With large displacements, the gripper is used to handle kiwifruit and at the same time determine its softness for sorting purposes. The designed flexure-based gripper exhibits large displacement that fall within the millimetre scale range. This paper presents a robotic gripper design which relies on flexural joints rather than prismatic and revolute joints to ensure gripping action. Further, it should support the designer to find the best compromise between these concurring goals, i.e. The goal of this article is to demonstrate which combinations of range of operation and task space stiffness are possible. It can be increased by an extension of the compliant section but this reduces the task space stiffness of the hinge, as with increasing compliance it gets prone to disturbance forces. The main limitation of flexure hinges is the limited stroke, because high stress is occurin for large displacements. However, there are limits for the use of flexure hinges. Figure 1 shows an example of a flexure hinge based positioning stage for small motions (work- ing area: planar rhombic form with 2302. The latter points can be achieved by flexure hinges, which predestinates them for mechanisms in high precision applications, micro manufacturing, micro electromechanical systems and others. Further, it should be free of frictional effects, back- lash and acoustical noise. for rotational joints low rotational stiffness and high axial and transversal stiffness. ideal hinge has zero stiffness in joint direction and infinite stiffness in blocked directions, i.e.
